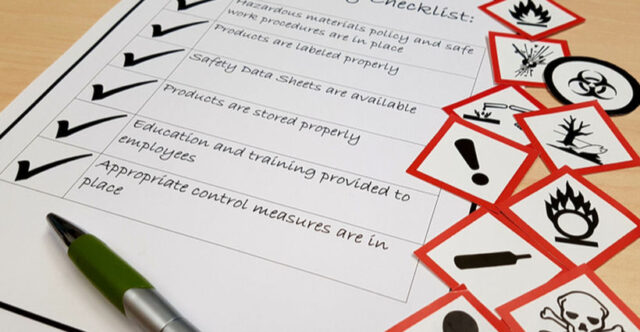
In a high percentage of businesses, people need to handle harmful chemicals. That doesn’t mean that all of them will be damaging solely to human health. It needs to be said that these chemicals can be damaging to the environment as well. So, handling these as best as possible should be among the priorities.
It doesn’t matter if we are talking about a small mechanic shop or a manufacturing plant that employs a lot of people, these standards should be followed as much as possible. As you can presume, these standards are prescribed in a lot of different international agreements. Understanding these is a must.
That’s why it is crucial to know how to maintain safety data sheets. If you are interested in having some professional help with these, click here. Now we would like to provide you with some tips that can help you with maintaining these on your own. Let’s take a look at some of these.
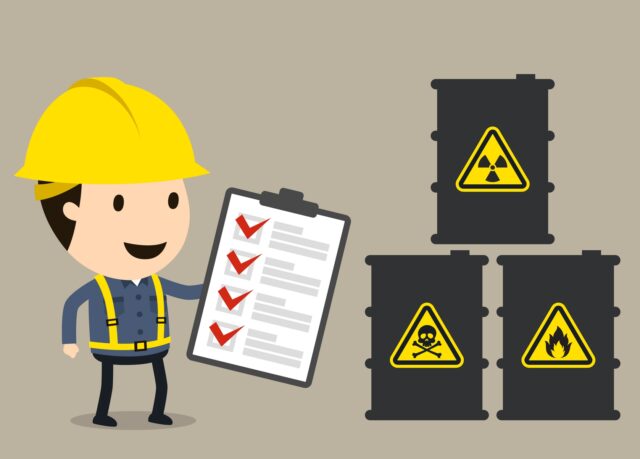
1. Update Them Frequently
The first thing we want to say is that having an effective safety data sheet has one crucial condition, they need to be kept up to date. The reason is quite simple, these standards are updated frequently, and you need to be aware of these changes whenever they are imposed. Doing this is an absolute must.
The reason why this is essential is the chemicals used in your workplace. There are three main ways when this can happen. The first one is when a certain product has been replaced with a new one, which requires the use of different chemicals. The next one is when your product needs to change its ingredients.
The final reason is when new substantial findings have been identified during the production procedure. Since we are talking about quite a complex topic, committing a department that will handle these changes is one of the first things you need to pay attention to. You can be sure of that.
2. Follow All the Standards
Before you are ready to update your standards, you need to be aware of them, right? For those who don’t know about them, these are referred to as OSHA communication standards. The idea behind these standards is to formulate the protocols properly. That way, those who work with them will know how to handle chemicals when needed.
Sure, the first idea about these is to prevent them from being harmful to people and the environment. Besides this problem, it is also something that protects the company from encountering some dangerous and hefty legal battles. Furthermore, it needs to be said that these standards are different for each industry.
Also, it is not a surprise that some industries follow much stricter standards, for obvious reasons. We are talking about laboratories and companies that offer products that consist of numerous chemical ingredients. That’s why you need to be aware of these standards when creating safety data sheets.
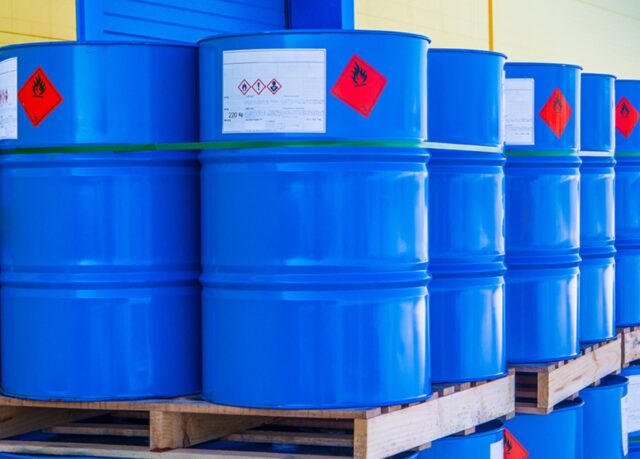
3. Labeling
The next aspect we want to talk about refers to the labeling procedure. Basically, it means that these labels should be put on all the shipping containers. Naturally, we are not talking just about labels that point out what chemical is inside these. Also, they should consist of some other information.
Besides the chemical itself, it should include all the precautionary methods in case something goes wrong. In some high-detailed labels, you can find information like how to prevent these chemicals from contaminating the environment when needed. Some would ask why are these needed if we have SDSs?
It is important since the transportation of these chemicals can be quite dangerous. So even the drivers need to be perfectly aware of how the transportation should be handled. For that reason, including labels as a part of SDSs is an absolute must if you ask us. We don’t doubt many would agree with us.
4. Educate Employees
SDS is crucial for the proper function of every company of this sort. However, employees should be aware of all the aspects to use them properly. Not to mention that employees should perfectly understand how to use all the tools at their disposal and how to remain safe during the process.
One way to do that is to hold meetings of this sort frequently. That way, employees will remain constantly about the postulates they should follow in each situation. At the same time, conducting training should be done to make everyone understand all of these rules perfectly.
We’ve mentioned that having a department in your company that focuses on these questions is a must. Another reason why this is essential is this training. Without understanding these, you cannot hope for having an equipped and trained staff that can answer all these questions when needed.
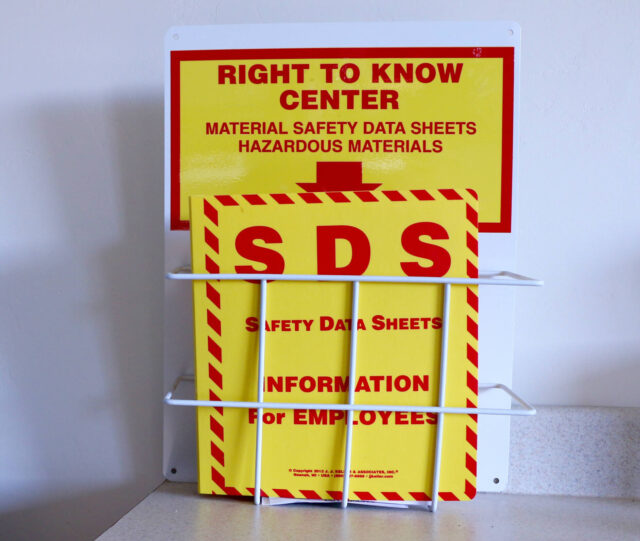
5. Proper Format
The final tip we want to talk about is putting safety data measures in a proper format. We cannot stress enough how essential this tip is. If you formulate them in a way that’s not readable by employees, then you cannot hope for a positive outcome. It needs to be as precise and strict as it can be.
A couple of decades ago, there was only one format. However, the times have changed in the last two decades, and we can see that a format known as safety data sheets was recognized as the best one by far. Some columns in this sheet are irreplaceable, while some others are mandatory, depending on the industry.
The format requires sixteen different columns. Among the most significant ones, you will find identification, first-aid measures, toxicological information, handling, and storage, etc. Including others depends entirely on the industry your business is in. Research these when needed.
Summary
Understanding how to set up safety data sheets is one of the priorities in many industries. Therefore, you need to be extremely careful about how you will implement it. In this article of ours, we’ve provided you with a couple of tips that can be of the utmost help in this procedure, both establishing and maintaining. Be sure to pay attention to these.